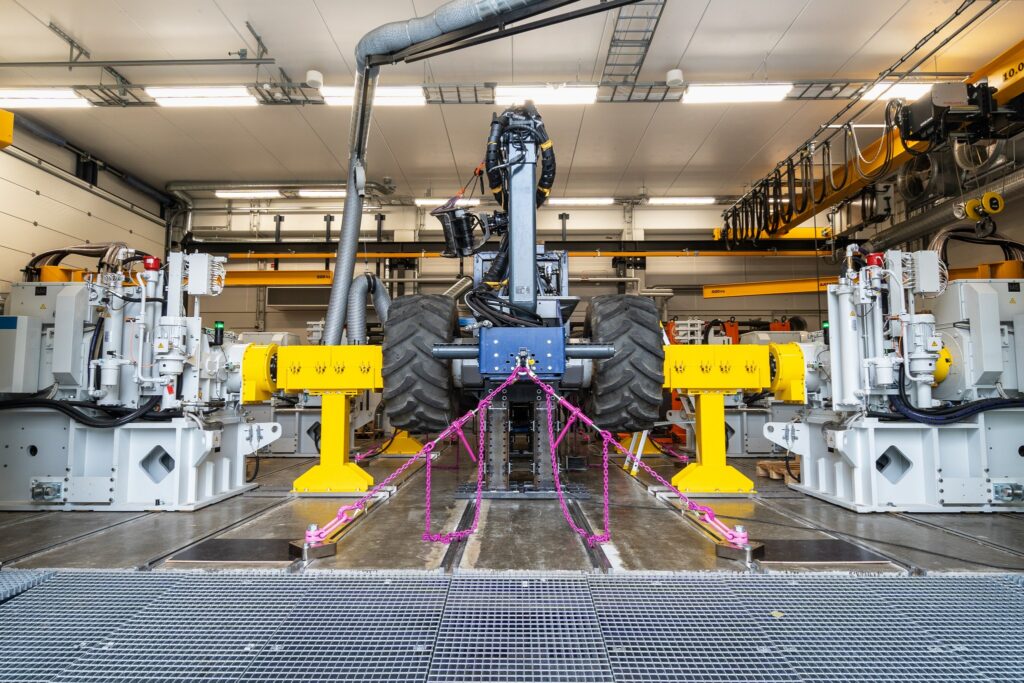
NUVE-LAB
NUVE-LAB is a unique research and development environment for energy-efficient, autonomous, and zero-emission work machinery and other vehicles.
Developing Autonomous and Environmentally Sustainable Utility Vehicles
NUVE-LAB provides an environment for industrial vehicle manufacturers to explore and develop carbon-neutral, autonomous work vehicles. We are working on ways to replace traditional, fossil fuel-powered engines with more environmentally friendly alternatives. Simultaneously, we are researching methods to improve the energy efficiency of equipment, for example, by promoting their autonomy.
NUVE-LAB is an open development environment that offers companies and research institutions an excellent platform for researching sustainable technologies needed to combat the impacts of climate change. The location on the Linnanmaa campus that is one of the largest university research communities in Northern Europe creates an outstanding opportunity for vehicle suppliers to lead the development of autonomous and environmentally sustainable vehicles.
Our advantage lies in the ability to create testing conditions tailored to the final operating environment of the work vehicle using Vehicle in the Loop simulation models.
Our technical field of expertise
- Testing proficiency, experimental measurements of driving events in the laboratory, and validation in field conditions.
- Data collection (sensing) and modeling of driving events, as well as data analysis and processing.
- Assessment of powertrain energy efficiency.
- Driving event simulation.
- Expertise in the development of electronic control systems.
- Modeling, digital twin, real-time simulation.
The environment is designed for mobile work machines and vehicles weighing up to 65 tonnes and with a power of 1.2 MW. The core of the system consists of a 4-wheel active dynamometer and an associated Vehicle In the Loop (VIL) virtual environment, where the final operating environment of the developed work machine can be modeled. The VIL extension enables the development and testing of work machines under loading conditions that correspond to the final operating environment.
Here's how our service works
Contact
Get in touch with our staff.
Needs Assessment
We will go through your needs and explore options for collaboration:
– Research project
– Paid service, priced according to usage needs
Scheduling
We will plan the implementation schedule.
Project Initiation
We will initiate the project.
Our facilities
NUVE-LAB, our research and development environment, offers research, development, and testing opportunities ranging from passenger cars to heavy-duty commercial vehicles. It is designed to support research and development of energy-efficient and autonomous vehicles.
Our laboratory is equipped with a Vehicle in the Loop (VIL) connection, enabling research in work machine technology under final operating conditions. Our modern laboratory aids in the development of vehicles that meet future market demands.
NUVE-LAB operates in line with sustainable development goals and practices responsible operations
NUVE-LAB enables a comprehensive range of load conditions that mimic various authentic operating environments. Testing of equipment for different operating environments can be carried out in the same location, without the need for extra transfers and the resulting resource and environmental impacts.
The development of NUVE-LAB has been guided by a vision of an ecological, economical, and socially sustainable research environment, where a digital simulation environment allows for comprehensive testing of equipment and machinery before transitioning to real-world conditions.
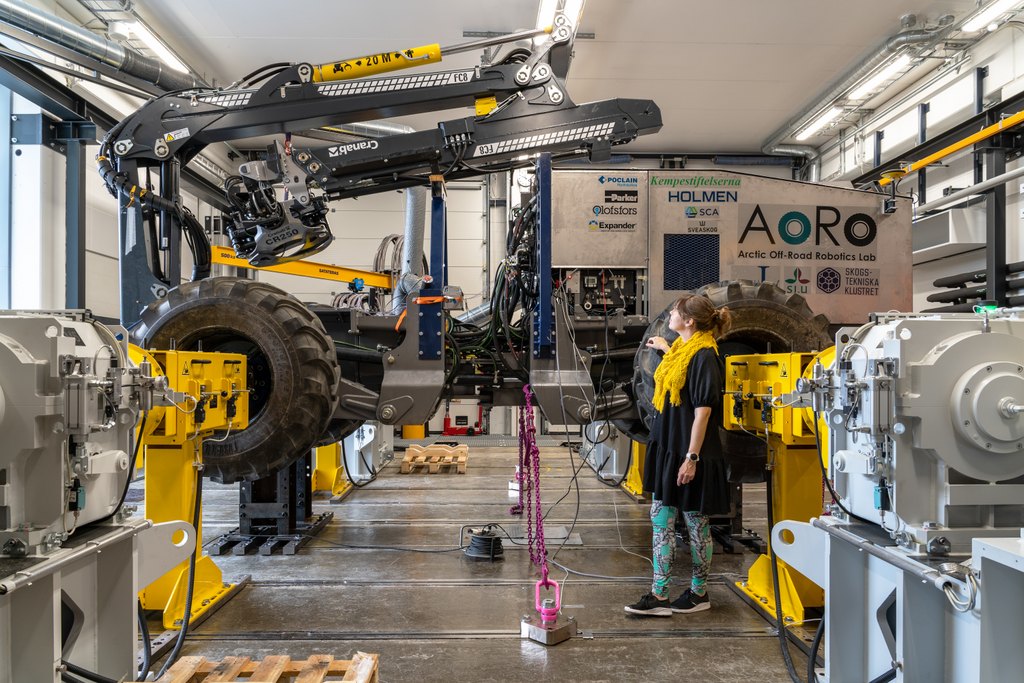
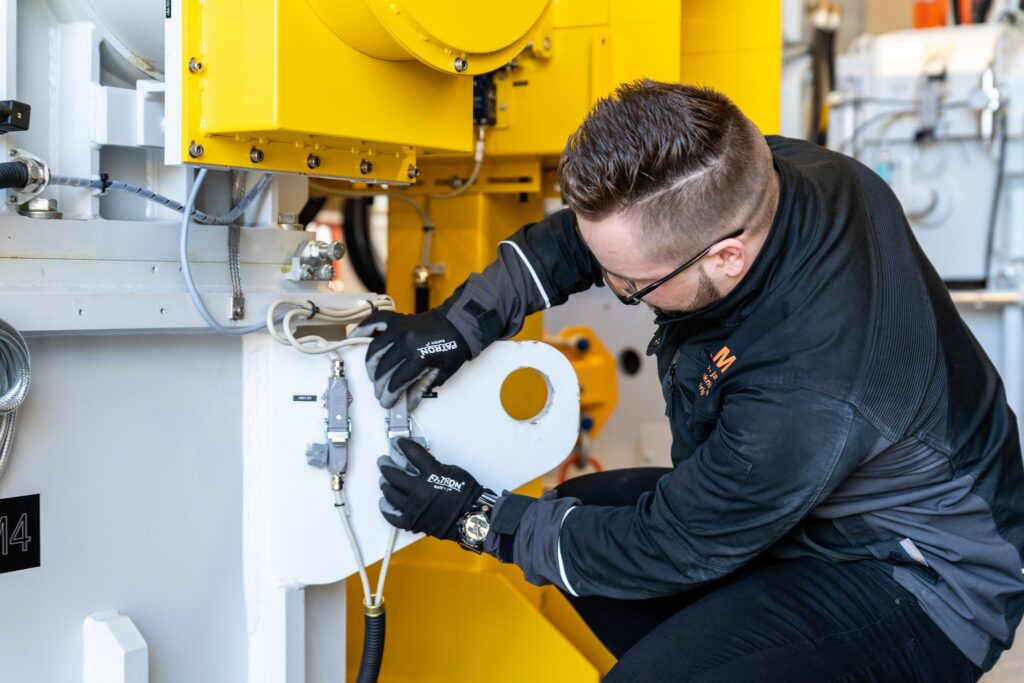

Through validation and calibration measurements of digital twins, we support the utilization of software-based simulation development. Simulation testing reduces the need to physically move machines from one place to another, directly impacting the reduction of carbon dioxide emissions, among other benefits. Simulations also enable the implementation of various tests and load experiments extensively, reducing the number of repetitions and variations required for final physical testing.
Digital solutions as part of promoting sustainable development and a clean transition are also part of the European Union’s dual transition towards green energy. NUVE-LAB supports the transition towards energy-efficient, autonomous, and zero-emission vehicles and work machines.
Our chassis dynamometer is hub-mounted. With hub mounting, the connection between the vehicle and the dynamometer is 100%, eliminating any slip or other rolling losses. Hub mounting is the best dynamometer solution for vehicle, user, and customer safety, as well as measurement accuracy and reliability. With an active dynamometer, we can emulate, for example, uphill and downhill driving. At NUVE-LAB, you can define various driving situations and work cycles by utilizing a modeled real work environment where the machine will ultimately be used.
Performance
Measure | Value |
Maximum nominal power | 1200 kW |
Maximum nominal power / wheel | 300 kW |
Maximum Torque (0-100 rpm) | 25 000 Nm, starting from October 2024, 100 kNm per tire. |
Rpm range | 0-2000 rpm |
Connection interface
Measure | Value |
Wheelbase | 1.3 m – 7.4 m |
Connection width | 1.8 m – 5 m |
Height position of the VUT (vehicle under test) axle | 600 mm – 1200 mm |
Height position of the PTO (power take off) axle | 600 mm – 1200 mm |
Vehicle dimensions and weight
Measure | Value |
Total weight | 65 ton |
Length | 12 m |
Width | 3.5 m |
Height | 4.2 m (maximum with tires) |
The dynamometer has been primarily funded by the European Regional Development Fund in Mobilab project.
04/2024 onwards NUVE-LAB will have in production a battery emulator. Emulator enables research and development of electronic drive trains and mobile work machines without installed traction batteries. This enables the research of various power line installations and technical solutions already in the concept phase. The battery emulator supports the determination of the required battery capacity without erroneous investments in expensive battery packs. This new system enables long continuous system reliability tests and safe modelling of failure situations without risk of accident in failure tests.
The deposited simulation models permit the emulation of:
- batteries, battery modules, battery packs and battery systems
- fuel cells, fuel cell stacks and fuels cell systems
- 400V -800V vehicle traction battery units
- All on-board DC power supplies in vehicles
Technology
- Bi- directional 2 channel DC Power supply with adjustable voltage/current dynamics uninterrupted zero crossing for instant switching between charging and discharging.
Power
- Totally 1000 kW continuous load to 2 independent channels enabling dual separate motor systems feeding eq. two driving axels in heavy vehicle.
Output voltage
- 10 – 1000 V
- Resolution: 16 bit accuracy
- Setpoint (Response Time): < 5 ms
- Including voltage drop compensation, through sense cables near DUT
Output current
- ± 1000 A
- Control resolution: 16 bit accuracy
- Current rise time: t90: ≤ 5 ms
- Ripple: < 0,1 % eff FS
- Setpoint (Response Time): < 5 ms
Control models
- Constant voltage (CV)
- Constant current (CC)
- Constant power (CP)
- Dynamic battery behaviour simulation via MATLAB/Simulink from external control system (e.g. real time simulation environment)
- Unloadable behaviour data from actual test drive
NUVE-LAB is equipped with an extensive measurement system and power analyzer, enabling, among other things, the production of efficiency maps (torque/rpm) from the electric powertrain and its components.
We are currently building capability to verify the energy efficiency of the work machine’s powertrain already at the conceptual level. Through this implementation, we will be able to test individual large electric motors as well. The facilities will be available in 2024.
From 10/2024, NUVE-LAB has in production a frequency converter suitable for controlling high-power electric motors. It enables examination and verification of electric motors and their load using axles and dynamometers at the system level. One of the most important advantages of the frequency converter is that the development and verification of different types of electric motors can be done before line production, and their efficiency maps can be measured and calculated for dimensioning and selection in advance in the concept phase. This new system enables long continuous pre-programmed system reliability tests lasting up to more than a day, including varying loads, acceleration ramps and safe failure modeling.
The frequency converter enables to drive:
- high torque permanent magnet motors, carbon brushless short circuit motors and synchronous reluctance motors (SynRM)fuel cells, fuel cell stacks and fuels cell systems
- motor powers up to 1100kW , constat current 1050A and peak start current up to 1300A
- air or liquid cooling motors
- preprogrammed system tests including emergency stop tests
Technology
- Bi- directional frequency converter having driving and braking functionality and power regeneration back to mains network
- Output frequency adjustable 0-300hz, enabling large variation of motor speeds
- Motor control having direct torque control (DTC)
- Torque control rise times: Open loop < 10 ms at rated torque, Closed loop < 5 ms at rated torque
- built-in safety system including the STO (safe torque off) system, EtherCAT and CAN field buses
Power
- Totally 1100 kW continuous load, 1300 kW in short time like in start up
Output current
- ± 1050 A nominal, + 1300 A max 10 sec, +35C
NUVE-LAB will be equipped with systems that enable the research of power sources and work machines powered by hydrogen and biogas. The capabilities will be built by the end of 2025.